
Orange Business: A leading network and digital integrator
Gain valuable perspectives from industry analysts on our market presence and solutions.
Explore our solutions tailored for your business
Our latest insights
A unique trusted partner
Orange Business is the Orange Group entity dedicated to businesses and organizations. Our unique history as a telco operator and now an IT services company enables us to support the sustainable digital transformation of enterprise businesses worldwide.
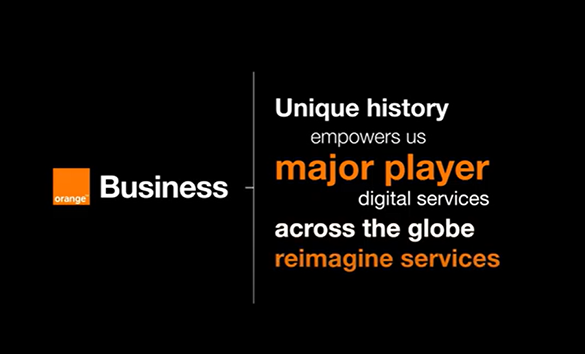
To view this video content, you must accept YouTube cookies.
These cookies make it possible to share or react directly on the social networks to which you are connected or to integrate content initially posted on these social networks. They also allow social networks to use your visits to our sites and applications for personalization and targeting advertising.
And figures show who we are
#1
World’s voice and data network
65 Countries
Teams presency on all continents
30,000+
B2B customers worldwide
5,500+
AI, Data and Cloud experts
6
Major Service Centers covering all continents